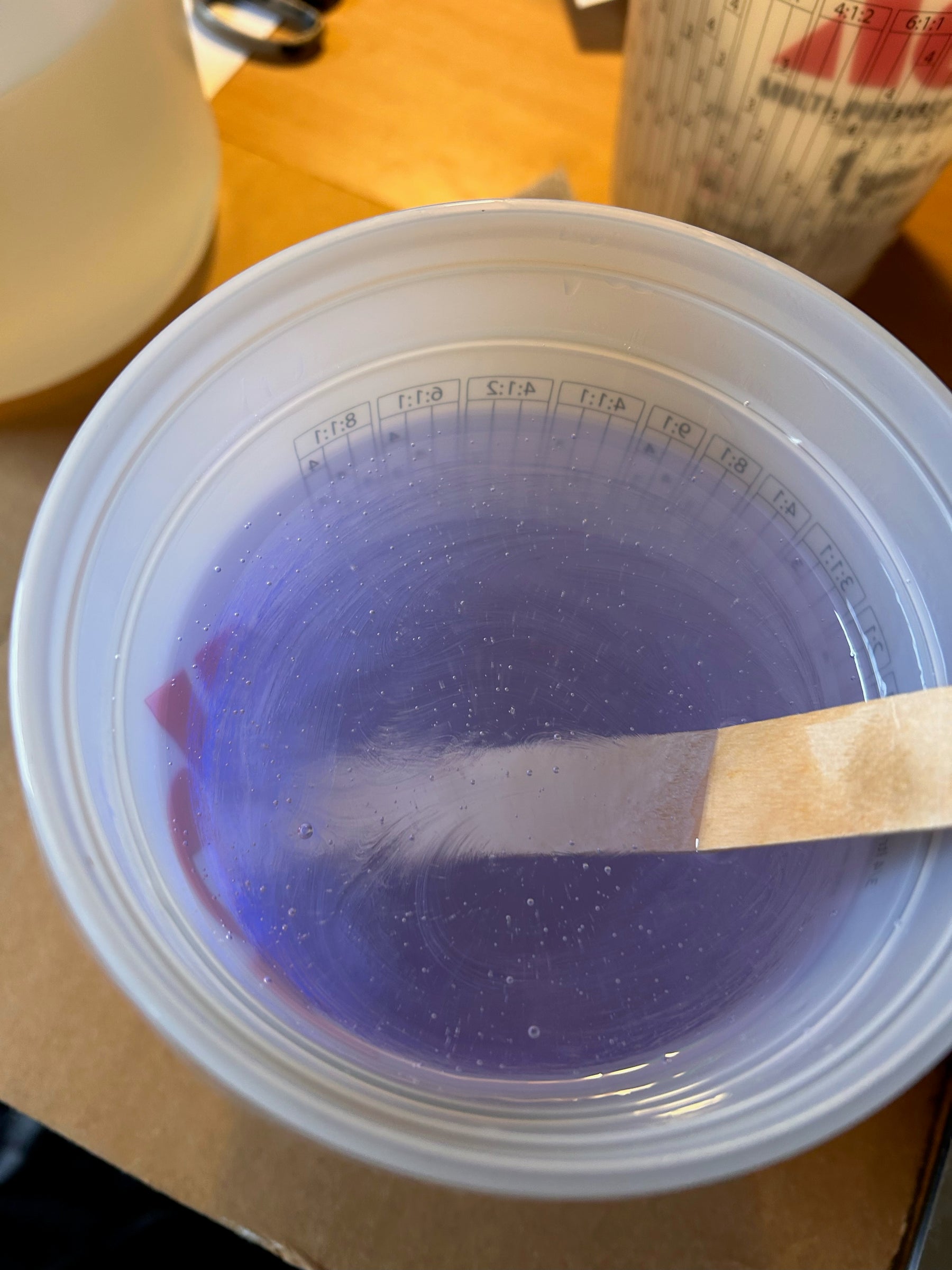
Fiberglassing with Epoxy Resin in Cold Winter Temps
Here are a few tips for fiberglassing with epoxy resin in the winter time when the temperatures are colder than you'd like...
Epoxy resin is temperature sensitive and its viscosity will thicken in cold as well as cure slower. Conversely, epoxy resin will be more water like and warmer temps and cure faster. Room temperature is optimal for optimal success with epoxy resin, especially in the seal coating application.
In the winter months, when it's colder the resin has increased viscosity making it slower to mix thoroughly and holds bubbles.
Heating the resin will decrease your pot life (working time) and it will exotherm faster... ideally you want the resin to be room temp (75-77F). Microwaving is quick and great but adds a lot of heat to the resin which decreases pot life.
When the resin thickens from being cold it's best to warm it up then let it cool back down to around room temp before mixing in the hardener. Slightly warm to the touch in the bottle is fine.
Also, it's ideal to have the blank at room temperature as well so there's no thermal shock when room temp resin hits cold foam or fiberglass... it's not a big deal but the seal coats come out nicer when everything's at a similar temperature.
Don't worry too much about bubbles, they will pop when the resin is laid out on the board. However it is best to avoid whipping the resin up and have the least amount of bubbles for the best finish.
And here's another little trick for winter glassing: You can do a quick hit with a heat gun to pop bubbles in the seal coat if things are a little too cold and start to thicken up and hold bubbles...